Technologies
NTx is enabling global access to tomorrow’s vaccines and therapeutics, today.
NTx’s continuous flow platforms for RNA / protein synthesis will address many of the issues and limitations found in current manufacturing methods. We offer a more adaptable and efficient production process to meet the demand for increased scalability and agility required to serve the use cases of tomorrow, today.
How NTx is Revolutionizing Biomanufacturing
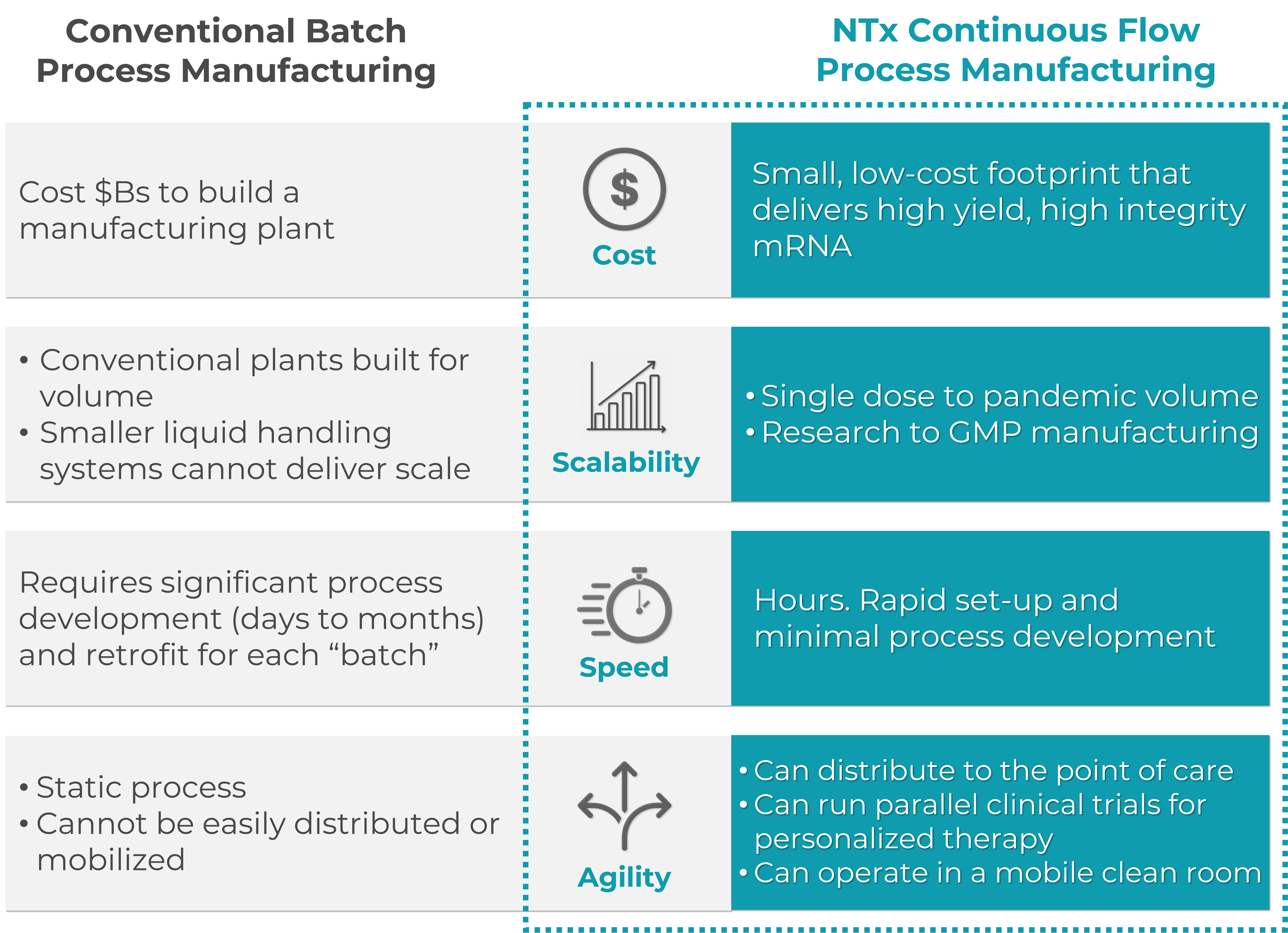
Reinventing Biomanufacturing to Improve Care
SPEED
Bench-top turnkey automated mRNA system processed >50mg of purified high-quality mRNA in a day
SCALABILITY
Continuous flow HFBR offers superior scalability from milligram to gram scale mRNA synthesis
AGILITY
Small footprint enables rapid deployment in portable or mobile cleanrooms
CONTINUOUS FLOW
Minimizes RNA product degradation and contamination associated with conventional batch manufacturing processes
Why Continuous Flow?
.png?width=1048&height=689&name=Slide%203%20(1).png)
- Single-use, closed system configuration to ensure product sterility
- Decreased shear and handling, minimizing product degradation and contamination
- Streamlines manufacturing operations by reducing batch unit operations
- Enables linear scaling from mg to gram scale
- Benchtop modular design can accommodate different drug substance formats in small scalable footprint
- Allows for integration of in-line process analytics